Due to the Corona Crisis, Holland Innovative’s seminar on “Data Science for Reliability and Root Cause Analysis” is postponed to 25 and 26 March, 2021. The event will show the best practices, latest trends, and innovations in open discussions and expert groups. Michael Pecht – founder and director of the Center for Advanced Life Cycle Engineering (CALCE), and Professor in Mechanical Engineering and Applied Mathematics, Statistics and Scientific Computation at the University of Maryland – is the keynote speaker.
Prof. Pecht advises small and large companies around the world on how they can integrate reliability into their processes. As someone who has written more than 20 books on product reliability, development, and supply chain management, Michael Pecht is one of the most renowned experts in the field of reliability. He has published over 900 technical articles and has authored a series of books on the electronics industry in China, Korea, Japan, and India. Prof. Pecht advises small and large companies around the world on how they can integrate reliability into their processes. So when Holland Innovative’s Hans Meeske started looking for the right keynote speakers for next year’s Reliability Seminar, there was one name that couldn’t be missed on the program.
Prof. Pecht says he’s happy he was asked to share his thoughts on the topic. “The importance of reliability has often been underestimated, but looking at the last 20 years or so, we have seen an increase in problems related to a failure of products like consumer goods, vehicles, and electronics. We’ve seen an astonishing amount of recalls, and consumers obviously feel this is not appropriate or what it should be.” These recalls are used as a defense against lawsuits, prof. Pecht says. “Companies accept that they suffer significant losses as well. They are willing to pay, but in fact, it moves the problem to the customers, who want a product that works and doesn’t have to be returned to the retailer.”
Can you trust your suppliers?
In a world that depends more and more on electronics, reliability is a vital element, “but a complicated one as well,” prof. Pecht adds. “The world is one huge network of connected systems. Value chains consist of several tiers of suppliers and distributors. The more you know about them, the better it is. But at some point, you just don’t know where your supplies come from anymore, let alone if you would want to buy from those companies in the first place. In such a situation, sustaining the reliability of your products becomes quite difficult.”
Prof. Pecht cites an example of this supply chain dilemma from his recent experience. “We were looking into a company that builds products using a battery pack. Of course, they knew who supplied these batteries, but what they didn’t realize is that this supplier had to buy the battery cells to build the battery packs with. It turned out that the problems they encountered were caused by bad cells. As a manufacturing company, you need to follow the chain to the very beginning, but in practice, this is not always possible.” Consequences can be serious: it’s not always just a toy or a toothbrush that simply stops working. “In 2018 alone, 19 battery explosions have been reported inside airplanes,” prof. Pecht explains.
The situation becomes even more complicated when you find out that suppliers often don’t know what the targeted application is. “In fact, most of them even don’t care to know,” prof. Pecht adds. “In a world where time-to-market becomes more important than ever and production standards are outdated and put together so that the community as a whole can pass, you can imagine this is a huge problem for reliability across the whole chain. Everybody in the chain wants to make more money, so there is a risk all over the chain. Can we trust all our suppliers? Small adjustments are being made all the time, without informing anybody further up in the chain. Managing the field of reliability is not an easy job.”
How can machine learning enhance reliability?
Michael Pecht’s Center for Advanced Life Cycle Engineering (CALCE) works with more than 150 companies from all over the world. CALCE’s research focuses on prognostics and systems health management (PHM) using machine learning. With PHM, it’s possible to look into the actual life-cycle conditions of a system, determine the initiation of failure, and mitigate system risks. PHM can yield an advance warning of impending failure in a system and thereby help maintain the system and suggest corrective actions.
Although the benefits of integrating reliability as an integral part of a company’s manufacturing processes seem like a no-brainer, this is not always the case. “It depends on the industry you are looking at, but overall I would say that it’s never enough,” prof. Pecht explains. “Some companies really do their best, but just don’t have the best people to perform the job. It immediately shows when we start asking them some very basic questions to which they are unable to offer the answers. Others just underestimate the importance of reliability all together. Typically, when these kinds of companies call us for help – and on average, we get 2 or 3 calls like that every week – something already has gone terribly wrong. The engineers can’t handle what’s going on and want us to help them explain the problem to the management.”
Delivering a “clean” product: Is it enough?
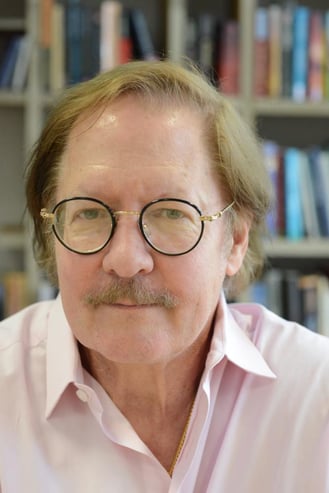
Michael Pecht
Although there certainly are differences between countries or even continents as far as the acceptance of reliability within a company’s processes is concerned, Michael Pecht is hesitant to say one company is performing better than the other. “You see differences between countries, between industries, and between single companies. And yes, some of these differences can be explained by local culture. In the US, for example, we are very litigious: the risk of lawsuits makes a company quite wary. In a way, this helps give reliability the attention it needs. But then again, companies are trading this off with recalls and warranties, so it’s not a real solution. Mainland China is way less litigious and though I wouldn’t want to say that generally, this leads to bad products, I really have concerns about the quality of their work. I recently visited more than 20 battery companies over there and honestly, I would hate to see the products of some of them end up in an article I would be using.”
“Data science can see things a human can’t”
Holland Innovative’s March 2021 event will connect reliability and root cause analysis with data science. “That’s a great focus,” prof. Pecht reacts. As an integral part of his research and consulting, he is already using machine learning and a data-driven approach that can incorporate statistical and probability theories in addition to data preprocessing and data cleaning (de-noising). This approach can determine a product’s failure risks, time to failure, and remaining useful life, as well as predict the moment when specific maintenance and repair actions should be taken to extend the life of the product. “Data science is a very big deal for us, for many reasons. It helps us gain knowledge when we are testing already. By pulling off data during the tests, we can see what really happens inside the electronics. Data science can see things a human can’t.”
However, it’s not about testing alone. Companies like Apple, Google, and Amazon are constantly gathering usage information via their consumer products, thanks to the numerous sensors in each product.
“Data analytic tools can capture information straight from the end-user. In fact, the product can monitor itself and in some cases can mitigate potential catastrophes on the go. You can imagine that this way of working can be crucial to the medical, energy, and aviation industries.”
Professor Pecht, who also holds 10 personal patents, is already looking forward to next year’s event, not only because he enjoys what he is working on and is eager to tell the world about it, but also because “it can’t be stressed enough that the field of reliability is way too important to be neglected. We need to educate and inform the industry. So I am delighted that Holland Innovative has taken the initiative for this important seminar.”